Lean Project Management: What Is It And Why You Should Be Using It?
The lean system was mostly used in manufacturing. But the methodology is now making its mark in the field of project management. If you're a project manager, a team leader, or even a regular employee, you need to know the core principles behind lean project management. In this article, learn all you need to know about it in greater detail.
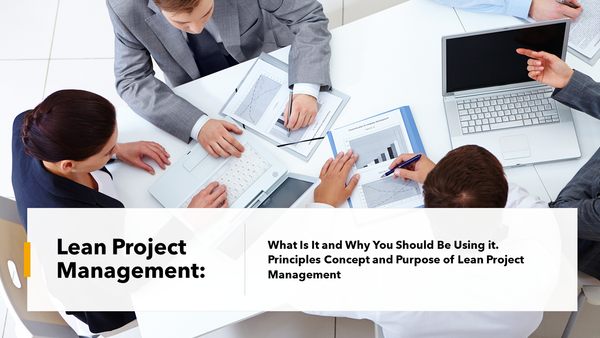
Principles Concept And Purpose Of Lean Project Management
Despite its growing adoption across industries, lean methodology isn't new. Its origins can be traced back to as early as World War II. Following the war's devastation, Japan's resources were scarce.
So they were looking for efficient ways for manufacturing goods. US sent a management consultant named W. Edwards Deming to help the Japanese make things in an efficient manner. His ideas about quality control to the development of lean methodology.
It is driven by five core principles which start with defining the value and end with perfection. Throughout the process, you keep on making improvements and minimize defects and waste. Most Japanese manufacturers and Toyota in particular, rigorously follow these principles in their practices.
The purpose of adopting lean project management was clear back then. And they still hold true to this day. Some of the purposes are:
- To reduce lead times or latency.
- To lower inventories.
- Reduce production and operation cost.
- Improve productivity.
- Enhance product quality.
- Increase profit margins.
- Increase customer satisfaction score.
You'll notice that the purposes mentioned above are interlinked. So if you reduce lead times, chances are you'll reduce your production cost too. Similarly, if you increase your customer satisfaction score, you may see an increase in profit margin as well.
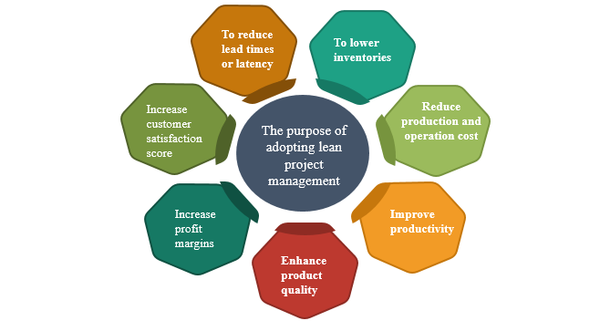
Lean Project Management (Lean PM) Principles
Lean methodology is based on five core principles. From manufacturing to service delivery to project management, these principles stay the same. The five core principles of lean project management are:
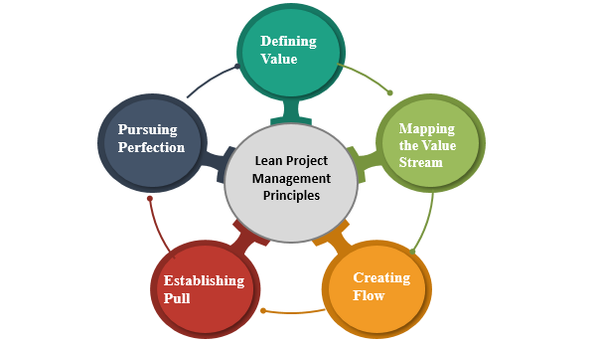
Let's explore each lean thinking principle in brief.
1. Defining Value
The first principle is about defining the value from a customer's point of view. The lean approach, it starts with the customer and his wants and needs. Then the team works its way in the most efficient way possible to meet his needs.
It's also important here to define what value means in this context. Generally, value is defined as the collection of features and benefits that the customer finds useful. The customer will pay based on the value he gets. So in a way, value is what the customers are willing to pay for.
In some cases, the customer might not even be aware of his needs. So you'd have to run through multiple interviews, surveys, prototype testing, and feedback loops before concluding what value means to the end consumer.
2. Mapping the Value Stream
The second principle is about mapping the value stream. It is the set of actions that the company takes to meet the customer's exact needs. You map the value stream by visualizing the steps and creating flow charts, blueprints, and/or spaghetti diagrams for the end product.
This principle enables team members to spot potential steps that are wasteful. You can then work towards removing them or replacing those particular steps. Waste reduction is one of the main goals of the lean-approach.
It's also important to incorporate third-party vendors and anyone involved in the supply chain when mapping the value stream.
3. Creating Flow
The third principle is creating a flow in the process. And the flow means the process is free from inefficiencies, roadblocks, delays, and wasteful efforts. It's seamless and productive.
You may not achieve this flow in one go. So you need to make several adjustments and conduct multiple pilot tests to reach the flow. But once you reach there, you'll realize an improvement in production and lead times.
4. Establishing Pull
The lean approach differs from the traditional management approach in that adopts a pull approach. In contrast, traditional practices adopt the push approach.
The pull approach makes the team more flexible towards inventory, which is considered one of the biggest sources of waste. You limit both the inventory and work-in-progress. This enables just-in-time delivery which is more efficient.
Since a pull-based approach is created keeping in mind the needs of the customers, they directly impact the customer satisfaction score.
5. Pursuing Perfection :
The final principle is the most important principle of lean thinking. It forces you to pursue perfection and never stop innovating. It makes experimentation and the efficiency-seeking process part of your corporate culture. So your company keeps on innovation quarter after quarter and exceeds your customer's expectations.
These five principles provide the framework for using the lean approach for your organization.
The Lean Project Life Cycle
Every project goes through a life cycle, and lean is not an exception to it.
However, there are several lean frameworks and methods that define the project life cycle, such as:
- Deming Cycle
- Six Sigma
- Kanban Cycle
The stages will be different for Deming Cycle than Six Sigma. But they're more or less the same. Let's look at the project life cycle if we follow the Deming Cycle. Developed by W. Edwards and inspired by Deming philosophy, it encourages the four following cycles or phases:
- Plan
- Do
- Check
- Act
The Deming Cycle is also known as the PDCA cycle. You start with planning and identifying the problem. Then you get to work and develop multiple solutions to address the issues. Then you check which solutions perform the best. Then you adopt it into your practices in the final cycle. These cycles are more beneficial to recurring projects.
Six Sigma has various methodologies with its own set of phases. And one of them is the DMEDI, which stands for:
- Define
- Measure
- Explore
- Develop
- Implement
As you can see, most of the cycles stay the same. The only difference in Six Sigma is you spend more time exploring the possibilities. Lean project management is recommended to everyone from newly-established startups to billion-dollar corporations.