What Are The Approaches To Quality Management?
Overview
Quality management plays a crucial role in any organization, regardless of its size or industry. The concept of quality management can be defined as the process of ensuring that goods and services meet or exceed customer expectations. To establish a competitive edge in the market, organizations must prioritize

There are various approaches to quality management that have been developed over the years, each with its unique characteristics and advantages. This article will explore the different approaches to quality management and their applications in various industries.
Understanding Quality Management
Quality management is an ongoing process in which an organization systematically seeks to improve the quality of its products or services. It is an approach that ensures that the products or services provided by the organization meet or exceed customer requirements.
The goal of quality management is to ensure that the processes used to produce products or services are efficient and effective, and that they consistently meet customer expectations. Quality management involves various activities such as identifying customer requirements, designing products or services to meet these requirements, setting performance standards, monitoring and analyzing quality data, and taking actions to improve quality.
The key principles of quality management include customer focus, leadership, involvement of people, process approach, continuous improvement, evidence-based decision making, and relationship management. Quality management enables an organization to deliver products or services that are consistent in quality, reliable, and meet customer expectations.
The Importance of Quality Management
Quality management is important for a variety of reasons:
- Customer satisfaction: Consistent quality products or services provide customers with a positive experience and reliability, leading to customer satisfaction and loyalty.
- Increased efficiency: Quality management ensures that processes are efficient and standardized, reducing waste, and errors and preventing rework, thereby making the business more productive.
- Cost savings: A focus on quality management results in fewer manufacturing defects, product returns and rework, leading to cost savings.
- Competitive advantage: By consistently producing high-quality products or services, a company can differentiate itself from its competitors and develop a competitive advantage.
- Compliance: Quality management ensures compliance with regulations, standards, and laws, reducing the risk of legal action and potential penalties.
Approaches To Quality Management
- Total Quality Management (TQM): TQM is an organizational approach that involves a continuous focus on quality improvement and customer satisfaction. It emphasizes the involvement of all stakeholders in quality efforts and the use of data and analysis to make informed decisions.
- Six Sigma: Six Sigma is a methodology used to identify and eliminate defects in a process, with the aim of achieving near-perfect quality. It relies heavily on data and statistical analysis to identify areas for improvement and to track progress.
- Lean Management: Lean management is a process improvement methodology that aims to eliminate waste and minimize non-value-added activities in a process. It involves identifying the value stream of a process and optimizing it to improve efficiency and quality.
- ISO Standards: International Organization for Standardization (ISO) standards provide a set of guidelines and best practices for quality management. These standards cover areas such as quality management, environmental management, and information security management.
- Agile Methodology: Agile is an iterative approach to project management that emphasizes flexibility, collaboration, and customer satisfaction. It involves breaking a project down into smaller, more manageable tasks that can be completed in short iterations, allowing for constant feedback and improvement.
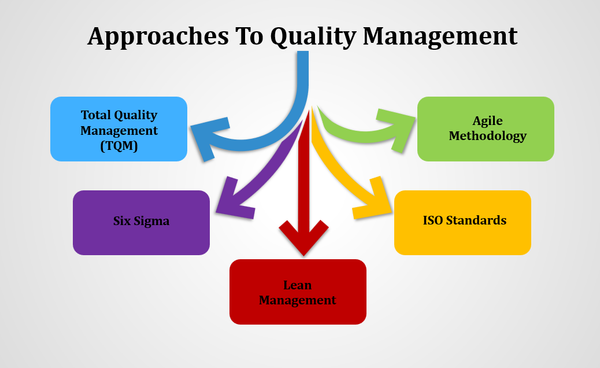
Total Quality Management (TQM) :
- Customer focus: Identifying and understanding customer needs and expectations to exceed their satisfaction.
- Continuous improvement: Constantly refining and enhancing processes and procedures to improve efficiency and effectiveness.
- Employee involvement: Encouraging and empowering employees to take ownership of their work and contribute to improving quality.
- Process approach: Focusing on the entire process, not just individual steps, to identify and eliminate potential deficiencies.
- Systematic approach: Adopting a structured approach to quality management, including planning, implementation, assessment, and improvement.
Six Sigma :
- Value: Identifying the value customers place on a product or service and focusing on creating that value.
- Value stream: Examining how the product or service is created and delivered to customers and identifying areas of inefficiency.
- Flow: Ensuring the smooth flow of work processes by reducing or eliminating bottlenecks and delays.
- Pull: Utilizing customer demand to drive production and delivery to minimize waste and avoid overproduction.
Lean Management :
- Value: Creating value for the customer is the first priority.
- Waste elimination: Eliminating waste is a key principle of lean management, and it includes anything that does not add value to the customer.
- Continuous improvement: Continuous improvement is a key aspect of lean management, which means that processes should be continuously analyzed, evaluated, and optimized.
- Kaizen: Lean management practices often include a focus on Kaizen, which is a Japanese word for continuous improvement and is an ongoing process of positive change.
- Customer focus: The primary focus of lean management is on the customer.
- Continuous flow: Lean management emphasizes the importance of creating a smooth and efficient flow of production through the elimination of bottlenecks and other obstacles.
- Just In Time (JIT): This is another important aspect of lean management, which involves producing goods or delivering services only when they are needed by customers.
ISO Standards :
ISO (International Organization for Standardization) has developed several standards related to quality management. These standards provide guidelines and best practices for organizations to establish and maintain effective quality management systems.
Some prominent ISO standards in quality management include:
- ISO 9001:2015 - Quality Management Systems: ISO 9001 is the most well-known and widely used quality management standard. It provides a framework for organizations to implement a robust quality management system (QMS) that focuses on customer satisfaction, process efficiency, and continuous improvement.
- ISO 9000:2015 - Quality Management Systems - Fundamentals and Vocabulary: This standard provides an introduction to the key concepts, terms, and principles of quality management systems. It serves as a foundation for understanding the requirements and implementation of ISO 9001.
Agile Methodology
Here's how Agile can be applied to quality management:
- Continuous Improvement: Agile promotes continuous improvement through regular inspection and adaptation.
- Collaboration and Communication: Agile emphasizes collaboration among team members, stakeholders, and customers.
- Quality as a Team Responsibility: In Agile, quality is everyone's responsibility, not just a dedicated QA team.
- Continuous Integration and Testing: Agile methodologies emphasize frequent integration of code changes and regular testing.
Conclusion
In conclusion, quality management is the process of ensuring that a product or service is meeting or exceeding expectations. There are several approaches to quality management, including Total Quality Management (TQM), Six Sigma, Lean, and ISO 9001.
Each approach has its unique characteristics and benefits and can be applied depending on the situation and goals of the organization. It is essential to integrate these approaches effectively into an organization's operations for successful quality management.